Charles E. Meyer Desalination Facility
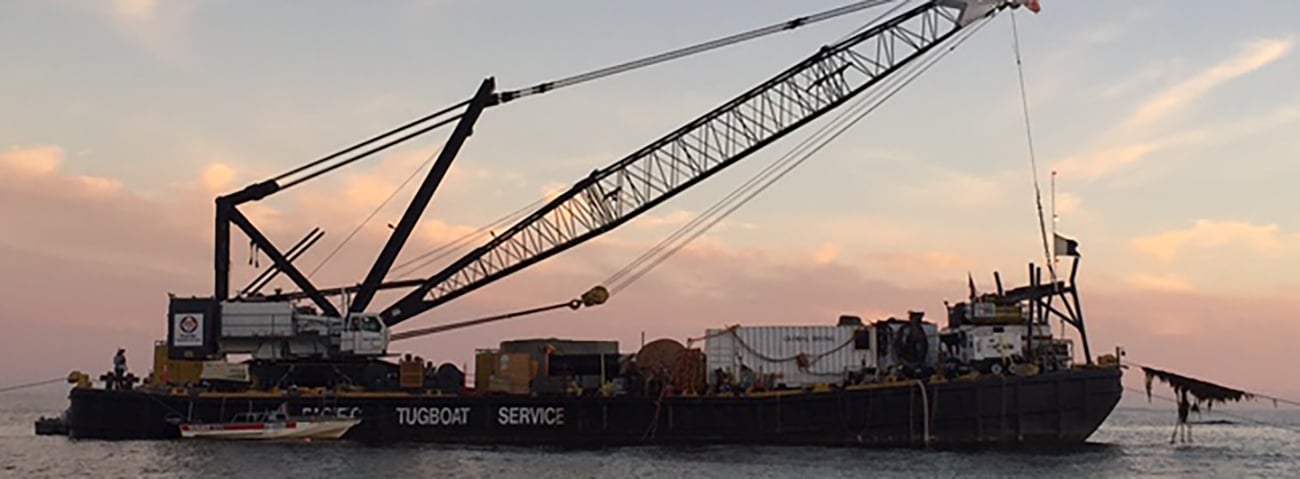
- HDPE
- Corrosion Resistance
- Ease of Installation
- Reliability
Against the backdrop of severe drought conditions across California, the city of Santa Barbara faced an extreme challenge: how to bring its Charles E. Meyer Desalination Plant back online after nearly two decades in standby mode. The project was further complicated by the discovery that an eight-foot section of the 36-inch subsea intake line, located 2,500 feet from the shore and under 50 feet of water, was missing.
Experts turned to Victaulic for a solution that included a grooved high density-polyethylene (HDPE) pipe with a specialized Style 908 coupling specifically designed to quickly join HDPE pipe and eliminate the need for fusing. Until then, not many engineers had used a grooved HDPE pipe for abrasive intakes, especially at desalination plants, given the corrosive nature of abrasive on metal used in traditional joining methods.
The Victaulic solution for the underwater environment offered extreme durability and reliability. Not only was the Victaulic Style 908 Coupling for HDPE pipe rugged enough to withstand the physically demanding operating conditions including corrosion risk, but it also provided reliability for the life of the system. To ensure the Style 908 coupling could withstand 100 years of underwater service life, the coupling housings were coated with fusion bonded epoxy to eliminate the risk of corrosion and 50-pound zinc anodes were affixed to the housing bodies to provide the necessary cathodic protection.
To complete the entire installation underwater, Victaulic needed to repurpose its cut grooving (CG) tool so it could groove the pipe end after being submerged. Traditional Victaulic CG tools require electricity and electric motors to run, posing a significant challenge for the team since their target was 50 feet underwater. Victaulic retrofitted a CG3500 tool to run on a hydraulic motor with a hydraulic power unit located on top of the barge, making it the preferred choice to cut and groove the subsea pipes.
One diver accompanied the CG3500 from the barge to the ocean floor. The pipe was grooved successfully in 90 short minutes. The coupling was installed within 30 minutes, with a total installation time of two hours. The self-aligning Style 908 coupling provided a quick and unique solution to the strong ocean currents that the diver was facing during the installation.
Now operational, the facility has the capacity to produce three million gallons per day. This is equivalent to 3,125 acre-feet of water annually, or approximately 30 percent of the city’s water supply needs.
External Links