Crestwood Gandor Saltwater Disposal Facility
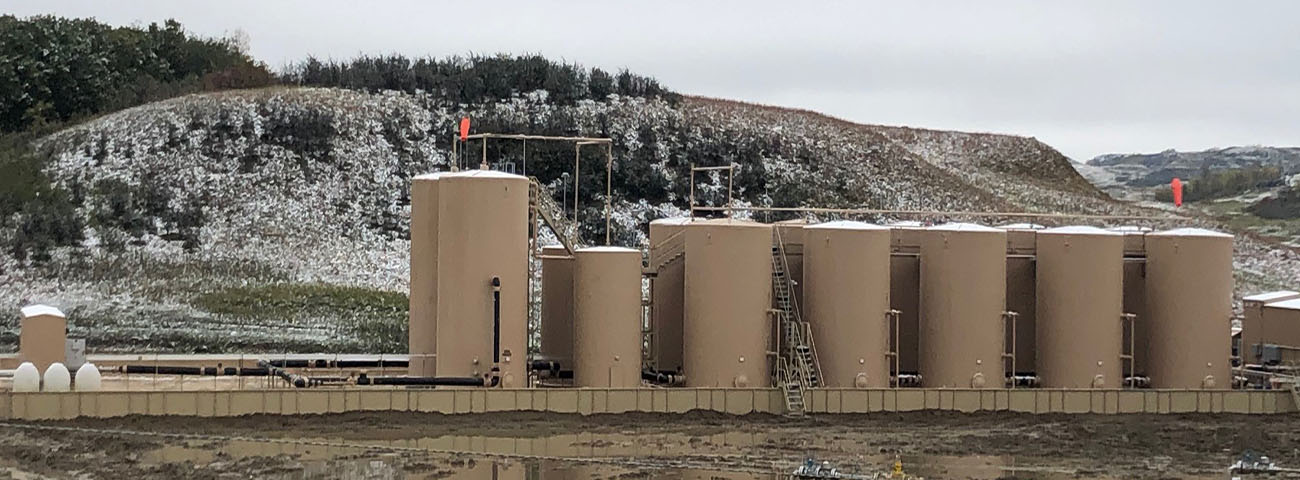
- Fabrication
- Virtual Design & Construction
- HDPE
- Compressed Construction Schedule
- Ease of Installation
Permitted to accept up to 50,000 barrels per day (b/d) of produced water, the Gondor facility features two wells, two separators, two oil storage tanks, and 10 produced water storage tanks across nearly three acres. When Crestwood began making decisions about how the SWD system would be constructed, three options were considered for the piping: stainless steel, fiberglass, and HDPE.
“HDPE was the best choice from a cost, constructability, and longevity perspective,” noted Mark Donnelly, a senior project manager at Crestwood. “Gondor is compatible with HDPE because of the way our system is laid out. There is a continuous inlet flow through the pipes that helps keep them warm, so even when we get those really cold North Dakota days, the cold won’t settle into the pipes.”
Construction on the Gondor SWD was planned to begin in the summer of 2019, well in advance of a contractual obligation to operate at partial capacity by October 1, 2019. As Crestwood’s producer customers continued to forecast growing produced saltwater volumes, it was imperative for Crestwood to identify an efficient option in order to keep the project under budget and manage the project’s tight construction timeline demands.
“That’s where Victaulic came in,” Donnelly said.
Victaulic’s vertically integrated fabrication solutions promised to deliver major productivity gains and labor efficiencies on the jobsite. In addition, their in-house Virtual Design & Construction (VDC) team worked with Crestwood’s engineering contractors to draft drawings for the Victaulic scope of work, consisting of 2-12” HDPE and internally plastic-coated carbon steel piping systems. Once completed, the design was imported into the overall project model and approved by Crestwood’s internal construction team.
Upon approval, Victaulic utilized one of its fabrication shops to assemble and ship pipe spools to the jobsite. The combination of Victaulic’s prefabricated HDPE spools and onsite fit-ups using Victaulic HDPE couplings required virtually no rework in the field.
Donnelly was impressed by Victaulic’s speed. “The way Victaulic’s project timeline was advertised to me was ‘three or four days to pipe up the entire tank farm once the spools arrive.’ If we had gotten just a typical contractor out there, cutting and welding or doing HDPE fuses, it probably would have taken them three weeks to do that number of fittings.”
On installation day, the joints were installed with minimal effort and maximum speed: 10x faster than fusing and flanging. The fabricated spools eliminated the need for field fabrication, removing field cuts and joint by joint assembly on site. Additionally, the Victaulic system eliminated challenging fitting-to-fitting fuses, as well as vertical and overhead fusing which is a virtually impossible task. The speed with which the facility piping was erected was astonishing, freeing up time for crews to move to other construction activities to help meet the demanding timeline.
Since the project’s completion, Donnelly said there have been no significant maintenance issues at the Gondor facility. “Crestwood will continue to consider Victaulic for low-pressure tank farm applications,” said Donnelly. “The efficiencies of the Victaulic approach are hard to beat.”
Award: PPI Energy Piping Systems Project of the Year
Published in: Making ends ‘meet,’ Oilfield Technology