HDPE System Solutions installed at Oklahoma Tank Battery
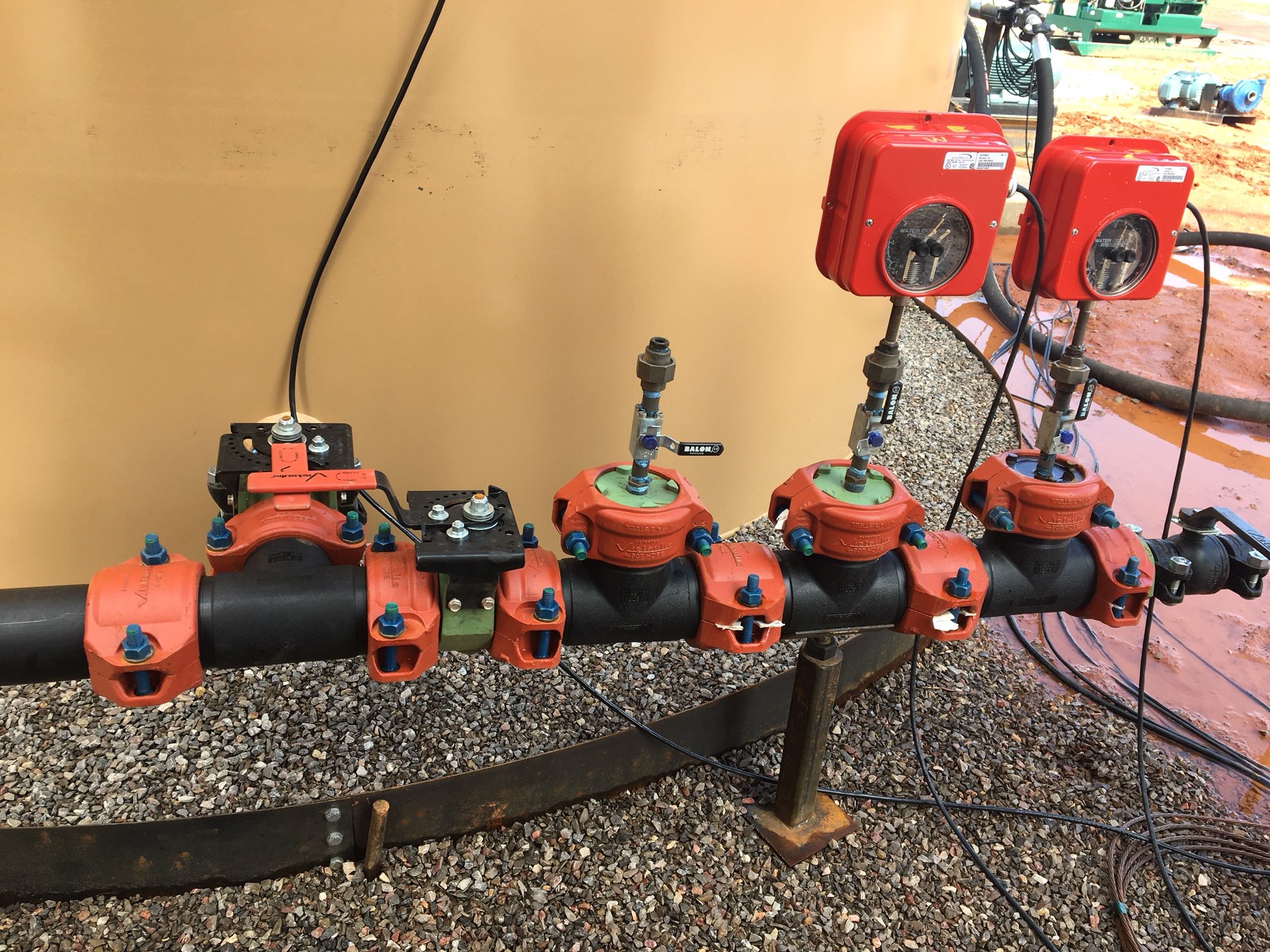
- Virtual Design & Construction
- HDPE
- Compressed Construction Schedule
- Corrosion Resistance
- Ease of Installation
A facility owner in Oklahoma began construction on a new tank battery, about a year after the reconstruction of an existing tank battery that had burned to the ground after being struck by lightning. Victaulic had presented HDPE system solutions to the owner prior to the reconstruction of the devastated tank battery, which resulted in time and labor savings on the initial system rebuild. As a result, the team decided to use Victaulic HDPE system solutions on all water applications within the new tank battery for quick and easy installation.
Victaulic Virtual Design and Construction partnered with the customer to complete detailed project drawings to streamline procurement and onsite installation, mitigating the risk of cost or schedule overages. The material was then shipped to the site according to the owner’s build strategy to optimize productivity throughout construction.
All oil facilities, separators, heater treaters, and oil tanks were piped with Victaulic Style HP-70ES EndSeal™ Couplings for plastic coated pipe, Internally Plastic Coated (IPC) fittings, and Series 727 Ball Valves. Along with this, the use of Victaulic system solutions for HDPE, including the Style 905 Coupling for HDPE, Style 907 Transition Coupling, and HDPE fittings, helped the owner to reduce their construction schedule by more than 3 weeks when compared to the previously installed fiberglass system. Partnering with Victaulic reduced the overall project schedule, enabling a full project completion in less than two weeks.